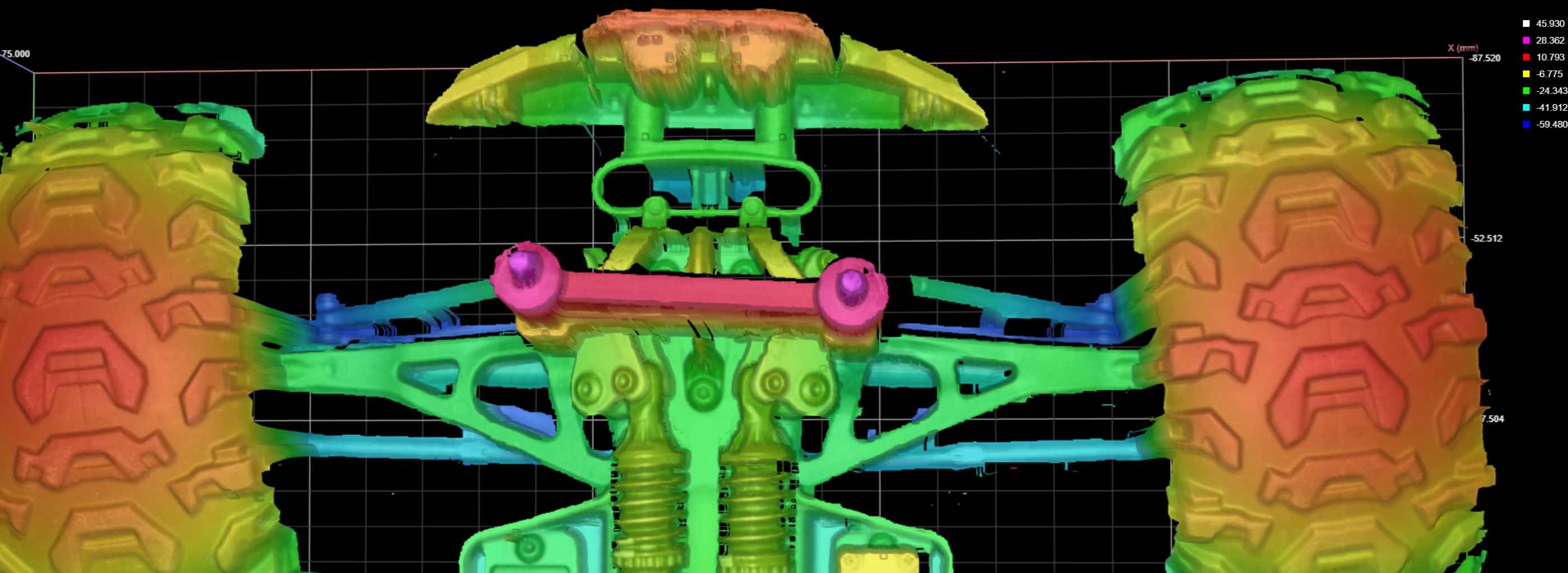
Systems
Overview and specification
of 3D Machine vision systems
3D camera solutions have become an important part of modern machine vision technology in recent years. They offer a number of advantages over 2D solutions. The colour or brightness of the object to be inspected is irrelevant.
The depth of an object can be detected independently. With 2D techniques, this information is not available, resulting in limited knowledge. Even small elevations or depressions, which are difficult to detect in 2D images, become visible.
3D MV systems enable more reliable detection of defects, such as cracks or deformations, because they capture the entire object in its spatial extent.
3D MV systems have become indispensable, particularly in the field of robotics. Thanks to the depth information, objects can be precisely located and gripped, even if the object information is tilted or superimposed.
3D = 3D?
Compared to 2D imaging, there is a wide range of acquisition methods available for obtaining 3D data.
Each 3D technology has its own characteristics, hardware requirements, costs and achievable accuracies, which can be very useful for certain applications. It is therefore worth taking a closer look at the subject!
Various 3D technologies:
-
Laser Triangulation
-
Structured Light (e.g. Fringe projection)
-
Stereo Vision (active / passive)
-
Time of Flight (ToF)
-
Confocal Imaging
-
Depth from Focus
-
Shape from Polarization
-
Light field
-
...
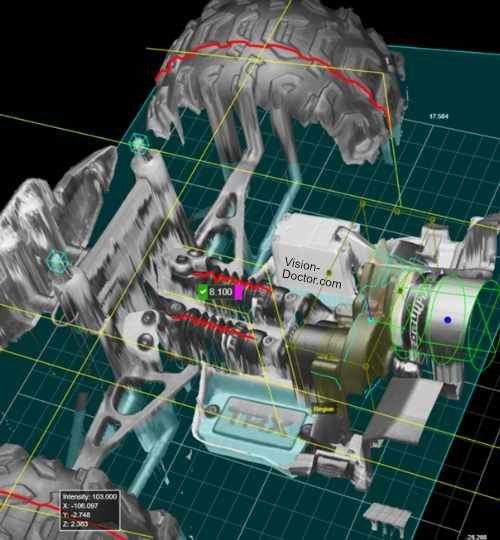
The world is a disk?
Today, most inspection tasks are still carried out using monochrome 2D camera systems. The reason for this is undoubtedly the ease of image generation with minimal effort. The reduced amount of data information is also often helpful when it comes to the fastest possible image processing.
However, this method is limited by the fact that the information is only displayed in one plane. It is therefore assumed that "the world is a disk". In reality, of course, this is not the case and difficulties arise during inspection.
Error sources for 2D imaging
-
Most objects are highly three-dimensional, not just flat.
-
The distance to the object can vary (thermal linear expansion is a sufficient source of error).
-
Objects can be slightly tilted (not parallel to the sensor) during acquisition. A slightly sagging plastic tray with objects etc. is a simple example of this.
This will introduce measurement errors which can only be partially compensated by telecentric measurement lenses.
2D image acquisition
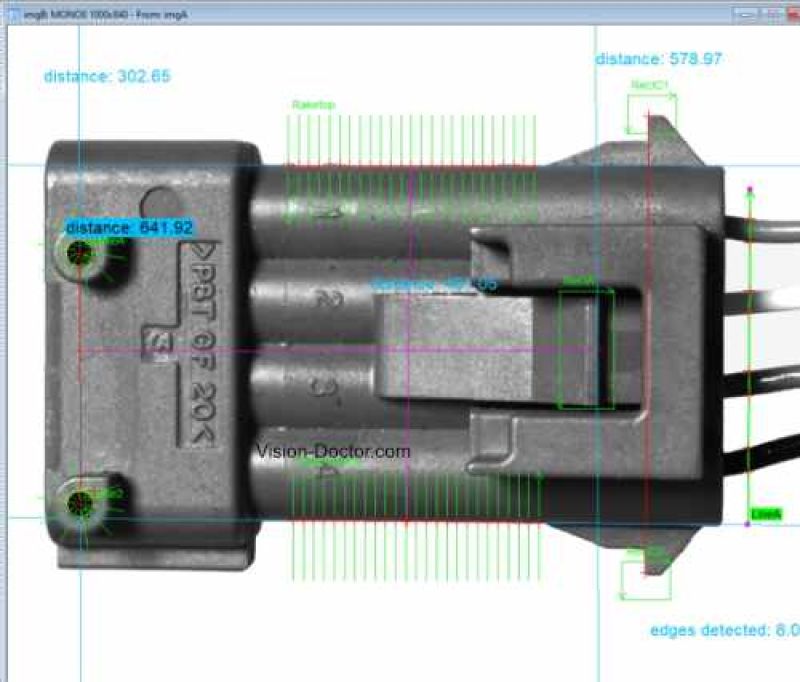
Advantages of 3D Imaging
The advantages of 3D imaging are obvious when comparing the two images: the features to be inspected are not only at different heights, but are also partially inclined. In a metrically calibrated image space, it is still possible to inspect correctly.
-
Features are detected independently of 2D grey-value contrast. Detection is based on 3D height information. This means that light and dark areas of the image or object information are also displayed as uniform 3D information that can be inspected.
-
In a calibrated 3D space, it is possible to work without scaling errors, even when measurements are taken at different z-distances.
-
2D image information: x, y, angle γ
-
3D image information: x, y, z, angle α, β, γ.
More information, fewer assumptions and compromises.
In many cases, the various 3D methods provide an additional intensity image that can also be analysed.
3D image acquisition

Selection criteria for planning a 3D camera system
The selection of a suitable 3D vision system requires the consideration of several key criteria. These factors help to ensure that the system meets the specific requirements and applications. Careful consideration of these criteria will ensure that the 3D vision system is optimally adapted to the specific requirements of the application. By selecting the right system, accuracy, efficiency and reliability can be maximised.
In short, a well-designed system works well!
1. Field of view (x, y and z)
The field of view determines how much of an object or scene can be captured. It is important to choose a 3D sensor with a field of view large enough to cover all relevant parts of the object. The x, y and z dimensions indicate the maximum size of the detection volume.
2. Motion
Another criterion is the ability for motion. A decision must be made as to whether the sensor should remain static or move to capture different perspectives. A static system is easier to implement, while a moving system can be more flexible to fully capture complex objects.
3. Needed resolution (x, y and z)
The resolution of the 3D sensor affects the accuracy and detail of the captured data. High resolution is particularly important for applications that require fine detail. Resolution is often specified in x, y and z and should meet the requirements of the specific application.
4. Free working distance
Free working distance refers to the area between the sensor and the object to be detected. An appropriate working distance ensures that the system can operate efficiently without the need to adjust the sensor or the object. It is important that the working distance is large enough to detect the entire object, but small enough to ensure high resolution and detail.
5. Dimensions, IP class, weight
The physical dimensions, IP rating and weight of the 3D vision system are also important selection criteria. These factors influence the integration of the system into the existing environment and its handling.
Especially in industrial robotics, a heavy sensor could cause problems with small robots. However, size and weight are also a serious problem in transport and drone applications.
6. Cycle time image acquisition & processing time
The cycle time for image acquisition and the time for data processing are critical factors in the overall performance of the 3D vision system. A short cycle time enables faster image acquisition, which is particularly important for industrial applications. Image processing time affects how quickly the captured data can be analysed and used. It is important to choose a system that provides both fast image acquisition and efficient data processing.
7. Type of material of the component
The material type of the object to be scanned plays an important role in the choice of 3D vision system. Materials can be cooperative (matte and opaque), glossy or transparent. Each material places different demands on the sensor and image processing algorithms.
8. Special features
Some 3D imaging systems offer special features such as texture image, multi-slope and HDR (high dynamic range). These features can improve the acquisition and inspection of 3D data and should be considered depending on the application requirements. Special trigger modes may also be features that are only available on specialised systems.
9. User skills
The choice of system also depends on the skills of the user. Smart cameras are often easier to use and are suitable for users with less technical knowledge. PC-based systems offer more flexibility and power, but also require advanced knowledge. What do you need?
10. Budget
Sometimes the potential investment costs are a clear priority. What is the best solution for a given budget? Again, there are often trade-offs to be made.
Need help selecting a system?
Vision-Doctor.com is a private, independent, non-commercial homepage project and not a technology provider or system integrator. Suitable technologies and further professional support can be obtained from the companies & partners listed below.
If necessary, I will be happy to provide a quick recommendation, contacts and brief information.
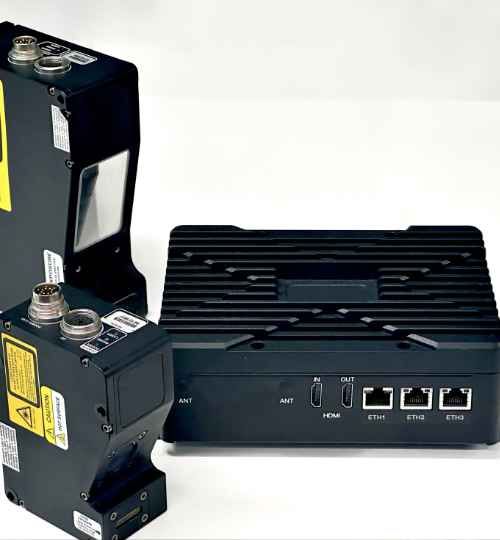