
Camera
Image transmission interfaces
An industrial camera usually transmits the image to a PC or embedded board for evaluation. There are many alternative interfaces and protocols for image transfer. New interfaces have been developed over the decades, making it difficult to keep track of them all.
Choosing the right transmission interface for industrial cameras depends on the specific requirements of the application. Factors such as data rate, range, latency and cost must be carefully weighed to ensure the best possible performance and efficiency.
Industrial camera interfaces

USB3 and USB3 Vision
USB3.x provides a flexible and cost-effective solution for image transfer in industrial applications. With data rates of up to 5 Gbps (USB 3.0) and 10 Gbps (USB 3.1), USB3.x provides fast and reliable connections. The ease of implementation and wide availability make USB3.x a popular choice for many applications. The USB3 Vision interface has also been standardised on the software side for configuration and image transmission across all manufacturers.

GigE Vision (1, 2.5, 5 & 10 GigE)
GigE Vision is a standard for industrial machine vision based on Gigabit Ethernet. With various speeds from 1 GigE to 10 GigE, GigE Vision offers a high bandwidth and range. This interface is ideal for applications that require fast and stable data transmission over long distances. GigE Vision is widely used as a classic industrial interface if the data rate is not too extreme.
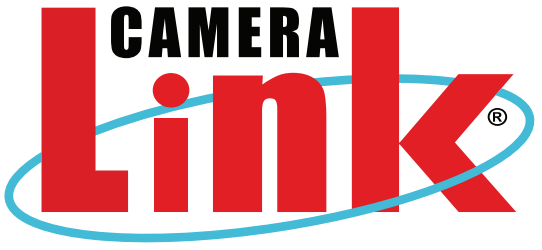
Camera Link (CL)
Camera Link is a serial communications protocol developed in the early 2000s specifically for machine vision. It offers high data rates and low latency, making it ideal for high-speed applications. Camera Link supports both parallel and serial transfers and is used in many industrial applications such as quality control and inspection. The interface is increasingly facing competition from 5 & 10 GigE.
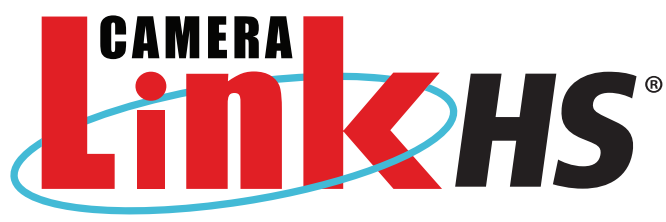
Camera Link HS (CLHS)
Camera Link HS (High Speed) is an evolution of the Camera Link standard, offering even higher data rates and distances. CLHS supports up to 10Gbps per channel and provides a reliable and stable connection for demanding image processing applications. It is used in many high-end applications.
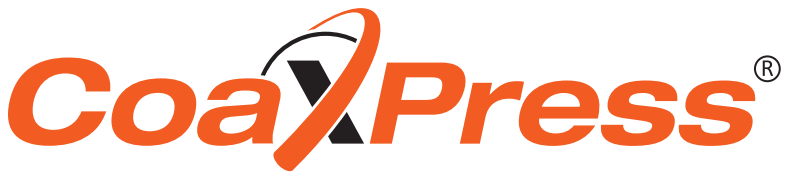
CoaXPress (CXP)
CoaXPress is a high-speed interface that combines high data rates with long cable lengths. With speeds of up to 12.5 Gbps per cable, CoaXPress is ideal for applications that require extremely high image quality and speed. For example, CoaXPress is widely used in the semiconductor industry and print inspection.
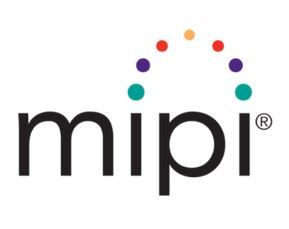
MIPI CSI2 for Embedded Boards
The MIPI CSI2 (Camera Serial Interface 2) is a common interface for embedded boards and mobile devices. It offers high data rate and low latency, making it ideal for applications with space and power restrictions. Used in just about every smartphone today.
Quick comparison of interfaces
GigE Vision
For more than 15 years, the GigE interface has been the quasi-standard for most 2D camera applications. Long cable lengths and cost-effective use of conventional network technology. The interface is now available with higher transfer rates (2.5, 5, 10 GigE) and is increasingly replacing Camera Link applications. Cameras can also be powered via Power over Ethernet. On the software side, the GigE interface has been standardised as GigE Vision (GenICam protocol), making it compatible with almost all manufacturers. The goal of GenICam® (Generic Interface for Cameras) is to provide a generic programming interface for all types of devices.
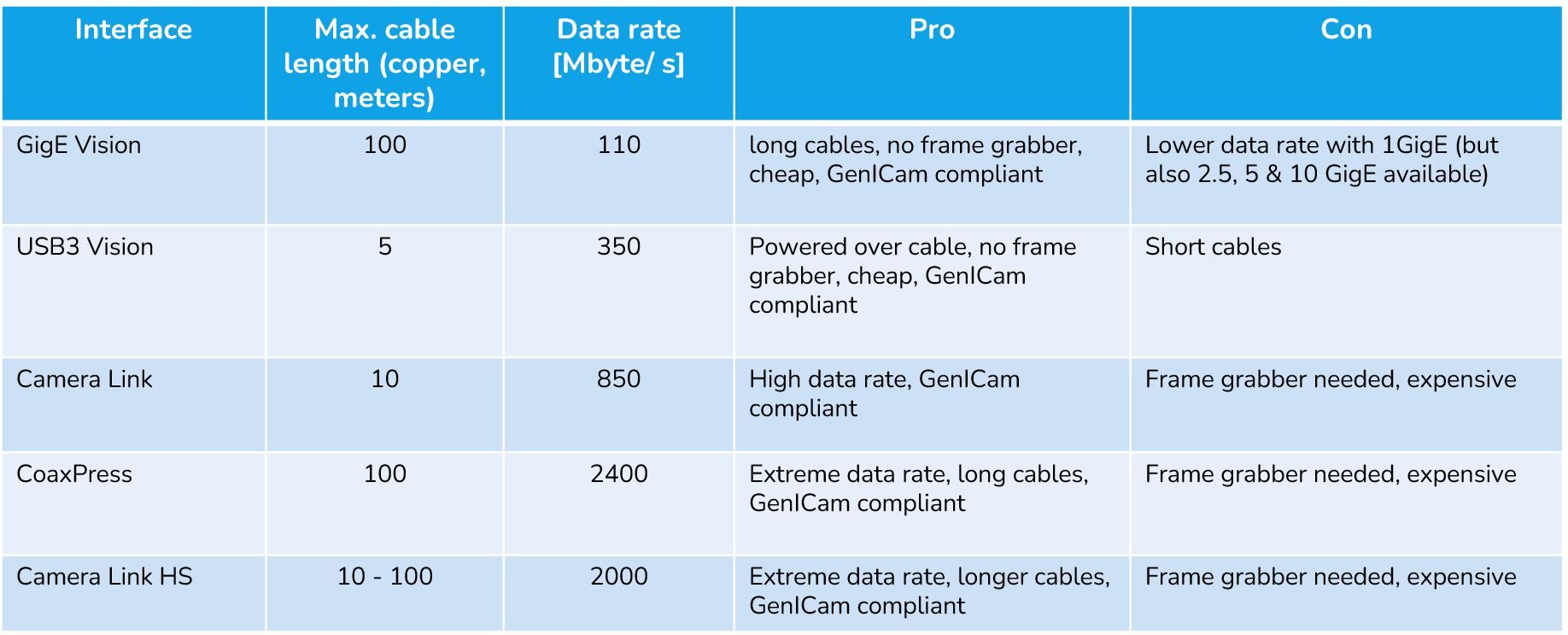
USB3 Vision
The energy-saving and cost-effective option for transferring image information of up to several hundred megabytes has found many friends.
Cameras are small, energy efficient and often cheaper than the GigE competition. Compact and good for designs with short cable lengths.
Camera Link
When it came to high bandwidths of up to 850 Mbytes/sec for line scan and high resolution cameras, for many years there was only one answer.
Today, it is under increasing pressure from simple solutions such as 5 and 10 GigE. Increasingly limited as a high-end interface, but still very reliable.
CoaxPress and Camera Link HS
High-end line scan camera systems with scan rates of up to 400 kHz or area scan cameras with 50, 120 or 250 megapixels require interfaces with extreme bandwidth that are also suitable for longer cable lengths. CoaxPress and CameraLink HS are available for these applications.
Complete overview of camera interfaces
Most industrial interfaces have been developed and standardised in recent years by international imaging associations in Europe, America and Asia. Further details on interfaces can be found at the American A3 Association:
https://www.automate.org/vision/vision-standards/vision-standards
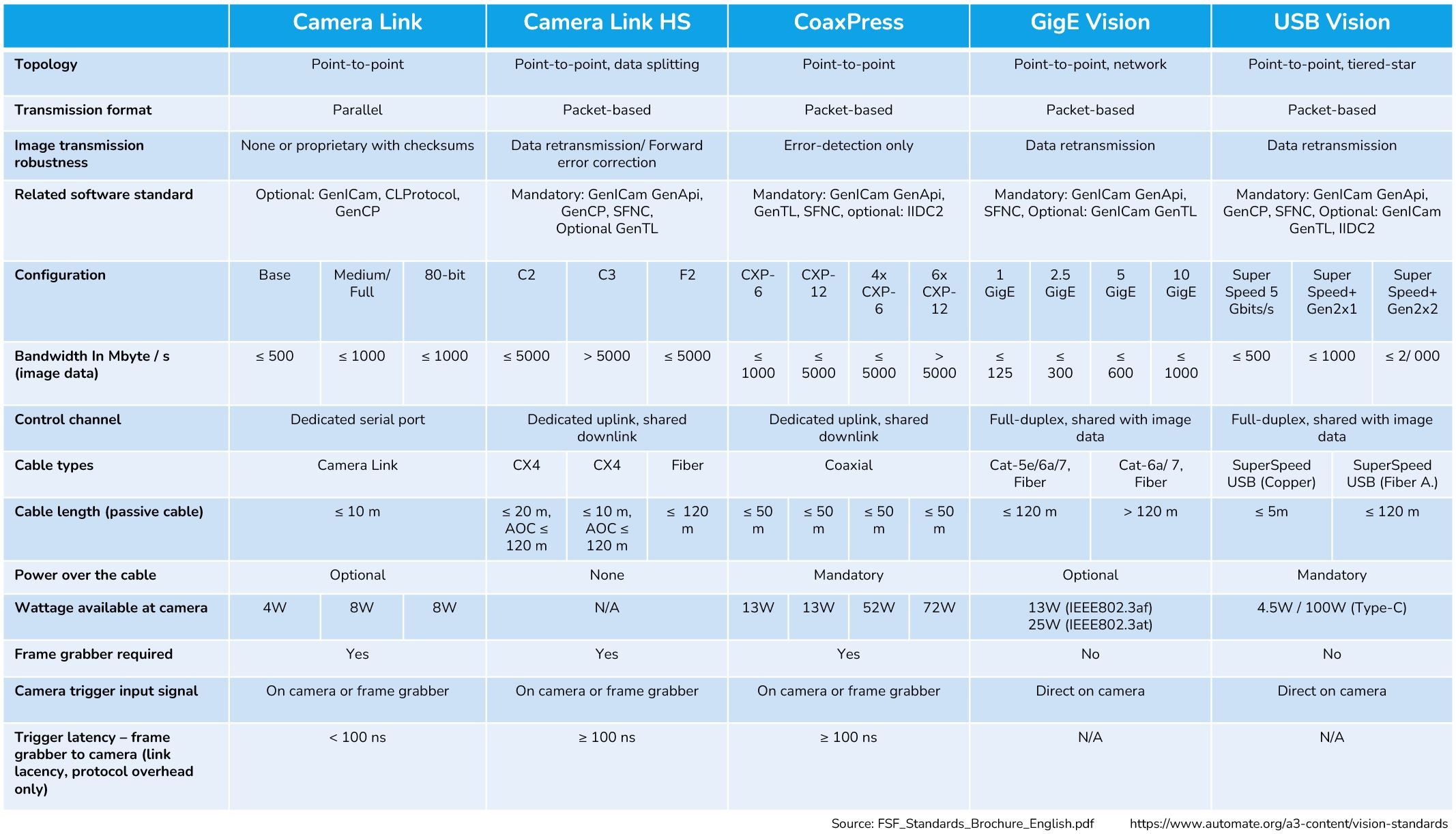
Additional communication interfaces
-
Digital inputs: These are usually used for camera triggering; with a line scan camera, line trigger signals are used in addition to an image trigger.
-
Digital outputs: These are used to directly control lighting synchronised with image capture, or to output a good/bad signal for quick part reject on the system, etc.
-
Encoder inputs: When scanning components with line scan cameras or 3D laser triangulation systems, the feed rate is sometimes transmitted to the camera with micrometre precision via encoder pulses. This allows a distortion-free image to be produced regardless of the speed of the line.
-
Serial interface: For industrial cameras, it is mainly used for parameterisation (setting of exposure time, gain, etc.); for smart cameras, it is mainly used for data communication with a PLC, etc. This interface is disappearing more and more.
-
Ethernet interface: In many cases, intelligent cameras are programmed and parameterised via the Ethernet interface, increasingly with Gigabit Ethernet. During subsequent system operation, measurement data and inspection results are sent via TCP/IP protocol to a computer, robot controller or PLC, inspection programmes are selected and even triggered if necessary. Images can also be sent to a computer system via this interface as a 'pseudo live image' for visualisation or logging. Other protocols, such as EthernetIP, ProfiNet and Modbus TCP, or specific proprietary robot protocols, can also be set up on this interface and can even run concurrently with the TCP/IP protocol. Compared to the serial interface, a much higher data rate is possible, as well as multi-communication.
-
LED indicators: Signal LEDs on the camera housing show the user the operating status (boot process, ready, busy, etc.) and provide information on triggering or data transmission. In some cases, these indicators can be freely programmed like a physical output in the camera to communicate specific information.
Need to buy the right camera?
Vision-Doctor.com is a private, independent, non-commercial homepage project and not a technology provider or system integrator. Suitable technologies and further professional support can be obtained from the companies & partners listed below.
If necessary, I will be happy to provide a quick recommendation, contacts and brief information.